How is the Nanobarrier Formed?
The substance contained in natural rubber that gives natural rubber battery separators their impressive technical advantages over other types of lead-acid battery separators has been identified and synthesized.
This page provides a description of how it works, background information, list of patents and reference publications.
General information
The primary function of a battery separator is to prevent electrical short circuiting between the battery plates - but a good separator is much more than just an efficient porous short circuit preventer. The North American lead-acid battery industry has known about the outstanding benefits of natural rubber battery separators for many decades. Natural rubber separators contribute electrophysically to the efficient operation of a battery. They give a better on-charge voltage characteristic, retard antimony "poisoning" of the negative plates and reduce the water consumption of aging batteries. Natural rubber separators are also surprisingly good at helping to reduce positive grid corrosion.
Lead-acid batteries fitted with natural rubber separators provide conspicuously superior performance compared to batteries fitted with other types of battery separators. Flat-plate positive plus rubber batteries can deliver a significantly higher power output and provide at least equivalent life expectancy to tubular positive batteries. There has been an upsurge in demand for this type of premium battery for deep cycling in essential service applications.
The world's largest lead-acid battery, 40 MWh load-leveling, Chino California, 8256 lead-acid cells, each rated at 3250 ampere-hours, fitted with flat-plate positives, special deep cycle grid alloys and rubber separators, provided indisputable evidence that this type of battery is not only capable of but quite easily managed to deliver more than 3000 deep discharge-charge cycles, (double the usual deep cycling maximum), by the time it was decommissioned as planned.
Technologies and Products
Antimony migrates out of the grids of the positive plates of lead-acid batteries to the negative plates during overcharging. Industry researchers have been proposing a variety of theories to explain how natural rubber separators retard this antimony migration. They appear to have overlooked, perhaps underestimated, the importance of the well known propensity of rubber separators to increase the negative plate top-of-charge potential. Take two identical fully charged cells, one with natural rubber separators, the other with polyethylene or PVC separators, connect them in series. Switch the current on and the rubber cell develops a measurably higher voltage. Switch it off and the extra voltage is gone. This is not electrochemistry at work but electrophysics. The rubber promotes a surface barrier on the negatives. A surface barrier that is only a few nanometers thick. It is physical and it is selective. (Similar principle to a reverse osmosis membrane.) It prevents antimony metal from electro-depositing on the negatives.
Natural rubber consists predominantly of cis-1,4 polyisoprene. Natural rubber contains small quantities of compounds that initiate the isoprene polymerization process in Hevea brasiliensis trees. These compounds are responsible for natural rubber's beneficial electrochemical effects on lead-acid battery functioning. It is simply an impurity that is present in natural rubber (and is not present in synthetic rubber).
Three distinct versions of Batteryvitamin based on natural as well as sythetic materials have been developed. The first, for use in battery refill water, has been in limited production since 2000 and full production since 2008. It is popular with supermarket warehouse operators. The second, which is patented - Copyrights, Designs & Patents - can be used in a variety of separators including UHMWPE/silica and PVC/silica, (included per masterbatches, pigments, fillers, plasticizers, stabilizers, etc). (There is an independent adaptation that is being used to boost economy-grade rubber performance). The third is incorporated in negative plates together with expanders. The first is soluble, the second has limited solubility and the third is insoluble. All three are highly mobile against the surfaces of negative electrodes, (plates), in sulfuric battery acid.
Established battery technology plus supplement - a winning combination
Natural rubber battery separators present a much higher electrical resistance to an ionic electric current in a battery than polyethylene separators. This represents a serious disadvantage for rubber, but rubber offers vastly superior battery performance in every other respect. Rubber separators have an electrical resistance of 300-340 mΩ per square centimeter. Hybrid rubber-polyethylene separators have an electrical resistance of 160-190 mΩ per square centimeter. Polyethylene separators have an electrical resistance of 40-55 mΩ per square centimeter. The electrical resistance of polyethylene is lowered very slightly by the addition of Batteryvitamin.
Natural rubber processing is labor intensive. UHMWPE processing is fully mechanized. A switch to UHMWPE-plus-supplement can translate into separator envelopes and mechanized motive power battery manufacturing. This can provide huge savings in battery manufacturing costs. Polyethylene battery separators sold in 2009 for $0.70 - $2.00 per square meter, hybrid polyethylene-rubber separators sold for $1.50 to $2.90 and pure natural rubber battery separators sold for no less than $3.00 per square meter. Commodity prices including natural rubber have fallen in recent years. This was temporary. Prices are rising again. It has been estimated that battery manufacturers specializing in flat-plate motive power batteries spent 4.5% of their total revenues on the purchasing of natural rubber separators in 2009. In contrast, it has been estimated that battery manufacturers specializing in conventional automotive batteries spent 1.5% of their total revenues on the purchasing of UHMWPE separators. Batteryvitamin can be readily integrated into an efficiency driven manufacturing process and can thereby have a strong positive multiplying effect on a company's financials.
The nanobarrier
The natural as well as synthetic versions of Batteryvitamin comprise a mixture of cylindrically shaped molecules that are sufficiently soluble in battery acid to migrate to both the positive and negative plates. They are destroyed at the positives but adsorbed end-on at the negatives - covering the surfaces of the negative plates with rod shaped molecules, generally as shown below. (The scale of the illustrations represents a magnification of about a hundred million times.)
The ends closest to the surface are in adsorption equilibrium, subject to attractive and repulsive electrostatic forces that act between the Batteryvitamin molecules and the surface, meaning there remains a tiny gap. This allows the battery related chemical reactions to proceed at the surface unimpeded and for the molecules to "ride" over the charging and discharging surface formations.
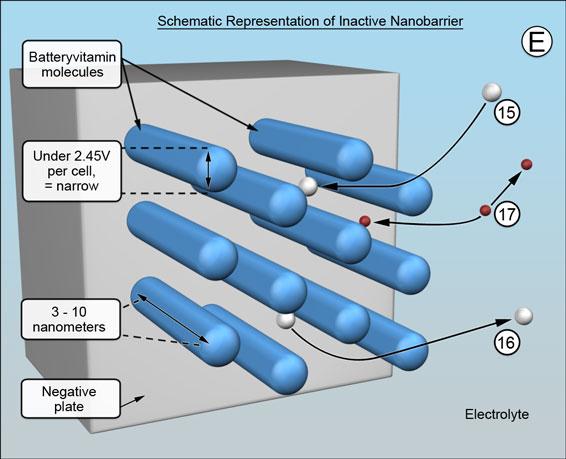
The barrier that is formed remains inactive while the battery is at rest, when it is discharging and is being charged - but not quite fully charged. The spacing between the individual rod shaped molecules is determined by electrostatics and will be wide enough for the battery process ions to move to the negative plate -15 and from the negative plate -16, and for the hydrogen ions to pass freely in both directions -17 , (E). (The mechanism of hydrogen ion migration being proton transfer, from water molecule to water molecule, a different proton being passed on very rapidly each time.)
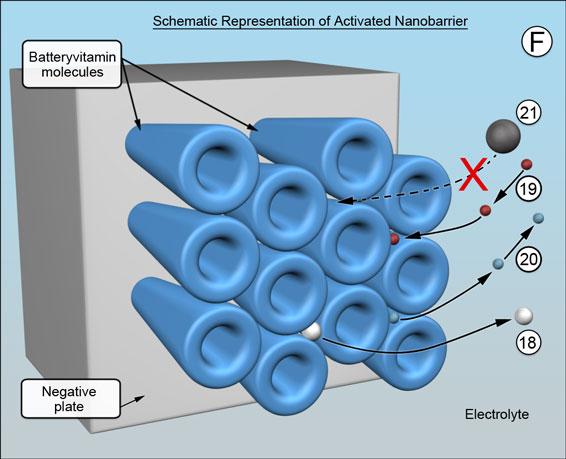
When the battery is being charged and is nearing full state of charge, there is the usual sharp increase in voltage and onset of gassing at 2.35 volts per cell. The rod shaped molecules charge their shape at 2.45 volts per cell, become effectively broader at their ends, which is shown schematically, resulting in the pathways between the electrolyte and the underlying negative plate becoming very much narrower, (F). The rod shaped molecules are voltage sensitive. The transition voltage is voltage activated. The transition voltage is preselectable between 2.17 and 2.50 volts by appropriate choice of molecules.
The barrier remains porous. As charging nears completion, the last few remaining battery process ions emerge -18. The individual pathways achieve their optimum size by "squeezing down" until a minimum sustainable threshold of hydrogen ion migration is reached. It happens across the entire barrier, ensuring the billions upon billions of pathways are all kept exactly uniform in size - barely large enough to allow fewer hydrogen ions to pass -19 and for nanobubbles of hydrogen gas to emerge -20, but too small for migrating metal ions to reach the negative plate-21. (Think of it as a self-assembling single-molecule-thick reverse osmosis membrane.) This causes the concentration of metal ions in the battery acid electrolyte to rise to saturation and, in turn, helps to minimize antimony "poisoning" of the negatives and to preserve the positive plates. (Metal ions do not exist in solution by themselves but are encased by a small cloud of water molecules, making them effectively much larger and easy to stop.)
Electrical testing and teardowns confirmed the essential spongy pore texture of the active mass in the negative plates to be unaffected by the low dosage Batteryvitamin substance.
Rubber
Theodore A Willard of Cleveland, Ohio obtained US Pat 761,345 on May 31, 1904 for a secondary storage battery with rubber separators. Rubber separators are therefore not a new innovation. Most of the rubber battery separator patents filed, technical papers and books published since the 1930s, (selection listed below), emphasize that the nature and mechanism of the ingredients in natural rubber responsible for the reduction in antimony transfer have remained unknown. Natural rubber battery separator technology has long been nurtured in the US. The challenges posed by the processing of natural rubber into an engineering product has, for many years, provided a significant barrier to entry. The battery separator industry seems to have grown into the habit of believing, "Why fix what ain't broke?".
Even if it ain't broke - fix it !
Technological change is the driving force behind the leading economies of the world. Patents form the most important class of assets in a modern industrial society. Patents are very dynamic assets which an owner can develop, license out or sell. All patents are published and full text copies can easily be obtained by searching online. Publication of a patented invention creates an awareness in the industry that a new technology, likely to be a better technology, has been developed. Awareness can initiate an unstoppable dynamic in the market place. Steven Sasson, a newly graduated engineer working at Eastman Kodak, was tasked by Gareth Lloyd, his supervisor, to develop a digital camera in 1974-1975. US Patent 4,131,919 entitled "Electronic Still Camera", was filed on May 20, 1977 and granted on December 26, 1978.
Kodak's management underestimated the extent to which digital would lower the barrier to entry to manufacturers with backgrounds in consumer electronics and cameras. Kodak should have immediately formed a partnership with one of the largest of these manufacturers, which would have bought them a significant headstart in the market place. They decided "photographic film would continue to dominate the market". In 1995 Casio of Japan launched the QV-10, the world's first consumer digital camera. Customers no longer wanted film after they discovered digital - and the company that had been founded by George Eastman in the 1880s with the promise, "You press the button, we do the rest", sold most of its patents to remain solvent and all but disappeared from the market place.
Kodak's management convincingly demonstrated that the real value does not reside in possession of title to a patent but in the new technology that it introduces to the business community. It does not take long for copies of published US patents disclosing new battery separator technology to arrive on the desks of battery industry decision makers around the world. They can ignore the technology or react to it. Work with the inventor or challenge the validity of the patent. A Patent Trial and Appeal Board was formed on September 16, 2012. It can be petitioned to challenge the validity of patents. PTAB has been described as favoring big business over the small inventor.
What appears to have been carelessly overlooked by the lawmakers and petitioners alike is that successful petitioners can find themselves at an unexpected disadvantage. Invalidated patents do not go away. All patent applications that have foreign counterparts are published and an invalidated patent represents free issue of technology, plus an instruction manual on how to use it, to manufacturers worldwide, including foreign low cost manufacturers. Invalidation gives them permission to flood the successful petitioner's market with low cost quality products that are exact copies of the invalidated patent. Nothing about patents is straightforward anymore.
If a lead-acid battery doesn't contain beneficial impurities - it won't work !
We may be inclined to forget and we must bear in mind that a lead-acid battery constructed of absolutely the purest lead, the purest acid and the purest plastics can only survive on light float duty but will definitely not work properly in everyday applications.
A battery must be deliberately made with "impurities" in order to provide a reasonable service life.
Antimony, calcium, tin, selenium, lignosulfonate, carbon and barium sulfate are "impurities" that have long been used by manufacturers. Polymerization initiator residuals and additives, that are inevitably present in battery separators, contribute more "impurities" that can affect the performance of a battery.
Cyclic voltammetry has often been used to measure the effect of natural rubber battery separators. Cyclic voltammetry uses three electrodes and applies a voltage that is ramped up and down linearly to make electrochemical measurements. Cyclic voltammetry can detect the effect of the active material in natural rubber on a cell in the presence of antimony but it is unable to assist in interpreting what it is or how it works. The following time-lapse movie shows a procedure that can.
Time-lapse movie
We have made a time-lapse movie showing the synthesized rubber supplement at work. Antimony transfer in a lead-acid battery cell consists of pure electroplating. The only way to prevent transfer is to prevent electroplating. The rubber and the synthetic alike prevent electroplating. The movie reveals the dendritic metal crystal growth that is typically obtained by plating from plain battery acid. Click movie image to view.
UNTREATED ELECTROLYTE SUPPLEMENT ELECTROLYTE
Our test rig consists of two beakers, with identical positive and negative electrodes, connected electrically in parallel, together supplied at 60 milliamps, constant current. Both beakers contain 1.250 SG sulfuric battery acid obtained from the same source. One part per million, by volume, synthesized rubber supplement was added to the acid in the right beaker. (Method used: Add 1 ml synthetic to 1000 ml acid, then take 1 ml of the mixture, add to 1000 ml acid, to give 1 ppm). Nothing was added to the acid in the left beaker.
We experimented with lead, antimony, tin, cadmium and copper, one at a time. The lead was so slow, it would have taken several months to complete. The cadmium and copper provided relatively coarse, substandard electroplating. The antimony took a week, adhering only briefly, then sliding off, forming a runny black precipitate. Antimony is unexpectedly, frustratingly not suitable for quantitative evaluation but fortunately, tin is an excellent substitute. The tin took eight hours to record and gave the remarkable results which we show in the movie. Naturally, we ran the test with rubber as well. The results were exactly the same. The untreated cell provided electroplating, the supplement cell provided none. We confirmed that rubber and synthetic can both be spectacularly effective at one part per million.
Our philosophy has always been "to make the footprints, not to follow in them". We do all our own research and development work. Please contact us if you have any questions about the technology/ product/ manufacturing/ marketing. It does not oblige you in any way.
Japanese ---- このページの日本語への翻訳はリクエストに応じて利用可能
Most of the patents listed below were filed only days before the patented products were put on the market, to maximize the effective life of the patents and were granted after the products had been on the market for some time. Most of the patents listed were pledged by the manufacturers, soon after they were granted, as collateral to secure loans from banks, to help build manufacturing infrastructures around the inventions.
US Patent 2,112,529 to Hazell; Eardley, (1938 - rubber plus clay, conventional vulcanization);
US Patent 2,120,281 to Hunt; Kenneth E, (1938 - rubber plus silica, conventional vulcanization);
US Patent 2,130,105 to Schaeffer; John A, et al, (1938 - converting agricultural waste into negative expander material);
US Patent 3,383,248 to Badgley; Donald V, et al, (1968 - synthetic polyisoprene, conventional vulcanization);
US Patent 4,213,815 to Goldberg; Bruce S, et al, (1980 - rubber plus silica, radiation vulcanization);
US Patent 4,224,393 to Feinberg; Stewart C, et al;
US Patent 4,327,164 to Feinberg; Stewart C, et al;
US Patent 5,154,988 to Choi; Wai M, et al;
US Patent 5,221,587 to Böhnstedt; Werner, et al, (uncrosslinked rubber as a separator additive);
US Patent 6,242,127 to Paik; Syng L, et al, (cured natural rubber in porous polyolefin);
US Patent 6,458,491 to Wimberly; Robert A, et al;
US Patent 6,485,867 to Navarrete; Jaime, et al;
US Patent 9,093,694 to Waterhouse, Robert R, et al, Battery separator composition that includes a polymer, silica and reclaimed rubber powder from road vehicle tires.
US patents, numerous, all lapsed, to Clough; Thomas J (et al), (Tried to "fence in" battery additive technologies by force of numbers);
US Patent Application Publication 2005/0058909 to Navarrete; Jaime, [abandoned], (grass lignin as a separator additive);
It has been known since the 1930s that separation sheets made of Hevea rubber provide superior lead-acid battery performance. There has evidently been a perception in the industry that rubber separation sheet manufacturing has excellent future commercial prospects, and in 2008 the leading manufacturer of polyethylene sheets purchased the leading manufacturer of Hevea rubber separation sheets. The purchase was ordered to be reversed by the Federal Trade Commission on the grounds that it was anti-competitive. The purchaser fought tooth and nail for five years to retain ownership, but the order to divest was upheld. We patented our inventions. One of our patent applications was published in late 2014. It identifies the impurity or active agent in Hevea elastomer, and provides details of equivalents in terms of a unique identity and quantity evidencing procedure. Our equivalents appear to have been accepted by the industry as the new gold standard for lead-acid performance, judging by the flurry of dozens of patent applications describing adaptations and modifications to our equivalents, that have been filed by separation sheet manufacturers, since 2014.
PCT/IB2008/003212, WO 2010/058240 to Mittal; Surendra Kumar, et al, [abandoned], (separator additive, to reduce water loss);
US Patent Application Publication 2010/0104946 to Deiters; Jörg, et al, [abandoned], (surfactant as separator additive - oxidation stability);
US Patent Application Publication 2010/0106468 to Deiters; Jörg, et al, [abandoned], (surfactant as separator additive - oxidation stability);
PCT/US2011/033263, WO 2011/133677 to Waterhouse; Robert R, et al, [abandoned], (vanillin in UHMWPE to control antimony transfer);
US Patent Application Publication 2011/0318629 to Ho; Marvin C, et al, [abandoned], (rubber as a separator additive);
US Patent 9,876,209 to Deiters; Jörg, et al, (surfactant as separator additive - oxidation stability) [numerous continuation applications];
US Patent Pending, Application Publication 2014/0255752 to Miller; Eric H, et al, (rubber as a separator additive - oxidation stability);
US Patent Application Publication 2014/0255789, US Pat 9,991,487, to Miller; Eric H, et al, (rubber as a separator additive - oxidation stability);
US Patent Application Publication 2015/0194653 to Waterhouse; Robert R, et al, [abandoned], (powdered tire rubber in UHMWPE);
Nanobarrier technology described on this page: US Patent 10,593,997. Continuations pending*. Chinese Patent ZL20140030287.0;
PCT/US2015/045060, patent pending, to Mittal; Surenda Kumar, et al, (surfactant additive);
PCT/US2016/012826, patent pending, to Mittal; Surenda Kumar, et al, (surfactant performance enhancing additive);
PCT/US2016/018217, patent pending, to Naiha; Mohammed, et al, (metal salt additive, surfactant performance enhancing additive);
PCT/US2016/019754, US Pat 9,979,054, US Patent Application Publication 2016/0254573, to Chambers; Jeffrey K, (separator additive, to reduce water loss);
PCT/US2016/035285, patent pending, to Perry; James Paul, et al, (rubber additive, surfactant performance enhancing additive);
PCT/US2016/046237, patent pending, to Miller; Eric H, et al, (surfactant performance enhancing additive);
PCT/US2017/305409, patent pending, to Perry; James Paul, et al, (rubber additive, performance enhancing additive);
US Patent 10,693,118 to Mittal; Surenda Kumar, et al, (surfactant performance enhancing additive);
US Patent Pending, Application Publication 2017/0054123 to Miller; Eric H, et al, (surfactant performance enhancing additive);
US Patent Pending, Application Publication 2017/0077479 to Miller; Eric H, et al, (rubber as a separator additive - oxidation stability);
US Patent 10,329,425 to Chambers; Jeffrey K, et al (fish meal as separator additive);
US Patent 10,396,330 to Pekala; Richard W, et al, (UHMWPE separators plus porous granules containing rubber and silica powders);
US Patent 10,673,099 to Chambers; Jeffrey K, (surfactant in battery separator for reducing water loss);
US Patent 10,811,655 to Naiha; Mohammed, et al, (broadly defined separator, including performance enhancing surfactant);
US Patent Pending, Application Publication 2018/0047990, and Continuation Publications 2020/0014030 and 2021/0320300, to O' Keeffe; Cormac, et al, [abandoned]. (The inventors claim a lead-acid battery that includes titanium dioxide in the grids, in the separators or in the electrolyte to suppress antimony migration);
US Patent Pending, Application Publication 2018/0366710 to Whear; J Kevin, et al, (separator designed to achieve multiple objectives with shapes and additives).
US Patent 11,152,647, to Whear; J Kevin, et al, (carbon and mineral additive). This inventor is named as co-inventor on about 80 patents and patent application publications;
US Patent Pending, Application Publication 2019/0058175, to Mittal; Surenda Kumar, et al, (surfactant and metal salt additive);
US Patent Pending, Application Publication 2019/0252665, to Chambers; Jeffrey K, (C(x) H(y) O(z) additives for reducing water loss);
US Patent 11,539,084 to Chambers; Jeffrey K, (surfactant in battery separator for reducing water loss);
US Patent Pending, Application Publication 2020/0295335, to Mittal; Surendra Kumar, et al, (non-ionic surfactant additives for reducing maintenance);
US Patent Pending, Application Publication 2020/0321580, to Perry; James Paul, (rubber plus non-ionic, anionic and cationic performance enhancing additives);
US Patent 10,270,074 to Natesh; Gubbi Krishnappa, et al, (non woven separators with natural rubber particles);
US Patent Pending, Application Publication 2021/0296737, to Perry; James P et al, (the inventors claim a membrane combined with water loss reducing and antimony poisoning mitigating additives that bear a remarkable resemblance to rubbers, additives and supplements previously disclosed by other inventors).
Some US patent applications* for inventions that involve polymer sheets plus surface actives, and that involve Hevea elastomer/rubber in one way or another, have been subjected to very long examination delays or very convoluted examination proceedings, while others sailed effortlessly through examination, suggesting a high likelihood of an absence of impartiality to outcome among some examiners.
Electrochemical Compatibility of Plastics - A.D. Butherus, W.S. Lindenberger, F.J. Vaccaro, Bell System Technical Journal, September 1970, 1377-1392;
Rubber Separators For Tomorrow: Performance Characteristics And Selectrion Guide - Syng L Paik, Giovanni Terzaghi;
The Influence of Rubber Separators On Electrochemical Behavior of Lead-Acid Batteries - Syng L Paik;
Evaluation of Hybrid Rubber-Polyethylene Industrial Battery Separators - Rick Wimberly, George Brilmyer;
Federal Trade Commission, File Number 081-0131, Docket Number 9327, (proceedings, court records, specifically 1. July 17, 2009 and generally 2. Sept. 10, 2008 to Dec. 18, 2013), Polypore International, Inc., Microporous Products, LLC. 1. (https://www.ftc.gov/sites/default/files/documents/cases/2009/07/090717resppropfofandcol.pdf) Pages 116, 163, 167, 186, etc; 2. (https://www.ftc.gov/enforcement/cases-proceedings/081-0131/polypore-international-inc-matter). COMPREHENSIVE MARKET SURVEY: The proceedings and records represent a systematic, effective, accurate and reliable determination of the nature, extent, product pricing, market share and revenues of US battery separator manufacturers, based on a 100% sample size.
Asahi Kasei Co. / 3M Co. / Polypore International, Inc., announcement February 2015 - Bloomberg - concluded August 2015.
Fundamentals of Electrochemical Deposition - Paunovic, M and Schlesinger, M, (The Electrochemical Society, Inc.), (John Wiley & Sons, New York, 1998), Chapter 10 section 2, Chapter 2 section 8;
Electrochemistry - Carl H Hamann, Andrew Hamnett, Wolf Vielstich, (Wiley-VCH Verlag GmbH, Wenheim, Germany, 1998);
Storage Batteries - George Wood Vinal, (John Wiley & Sons, New York, 1924, 1930, 1940, 1955);
Lead-Acid Batteries - Hans Bode, (The Electrochemical Society, Inc.), (John Wiley & Sons, New York, 1977);
Electrochemical Power Sources - Monty Barak, (The Institution of Electrical Engineers, London and New York), (Peter Peregrinus Ltd., Stevenage, UK, 1980);
Handbook of Batteries - Edited by David Linden, (McGraw-Hill, Inc. 1984, 1995, also edited by Thomas B Reddy 2002).
Bedeutung der Löslichkeit von Elektrodenmaterialien für die Kinetik poröser Elektroden - Klaus J Vetter, (Univ. Berlin), (1973), Wiley Online Library - requires login, institutional password for complete document: "http://onlinelibrary.wiley.com/doi/10.1002/cite.330450418/abstract", or Google via "Translate this page". (Excellent mathematical analysis of lead's ample mobility on porous conducting surfaces at nano-scale, hence explaining why the lead-acid concept works, despite the very low solubility of lead in sulfuric acid electrolyte.)